Lean manufacturing techniques focus on the systematic elimination of waste in a system with the aim to cut allinclusive lead-time; all while producing at the pace of buyer demand. For associates that strive for this ideal state, kanban-pull systems are very beneficial in helping us get there. However, like any other management belief lies a misconception about how to implement or what we are surely trying to achieve. Many years ago, several books were published touting the accomplishments of associates that have achieved so-called "zero inventory" or "zero potential control". It is simply fabulous what these associates have achieved. It is even more fabulous to watch other individuals surely take the term "zero inventory" and generate policies nearby the words themselves. I have personally seen managers bleed off stocks so that they could claim lean achievement since they "hold zero inventories.' Or, one company that has learned their episode the hard way, practically eliminated their potential control division because a consultant belief 'zero potential control' surely meant having a barebones potential department.
As crazy as it seems, these things happen for a easy reason: we fail to learn the underlying system and skills required in order to turn the concepts from ideas into policies and action. So, what then is the underlying principle behind "zero inventory"? simply put, zero inventory means that we have zero excess inventory. From a perspective of continuous improvement (Ci), we reconsider excess inventory a deviation from a set standard. As we arrival stock out situation (literally zero inventories!) this too is seen as a deviation. We then seek out ways to understand why this is happening and then bring the current conditions back to approved (pre-determined whole of production signals, or kanbans) further work must be done to preclude this deviation from happening again.
There is a saying that when we lower the water level (inventory) in the riverbed, we begin to see the rocks (problems) that impede the flow of good goods trying to make their way to the customer. The new system is more sensitive, with more problems than we have ever seen before. What does this sensitive system force us to do? Solve problems. Deviations in stock levels are good indicators of waste in the system. With fewer inventories in the system, we run the risk of denying our customers on-time service or delivery. With more inventories in the system, we run the risk of losing cash interests and not being efficient with our operations costs. It is truly a balancing act, but that's why we furnish to the rhythm of buyer consumption.
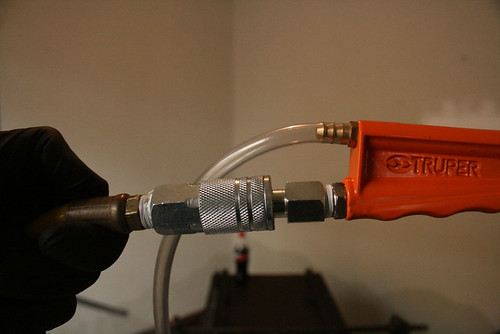
Quality departments are an additional one victim resulting from blatant misconceptions of 'zero potential control'. Although many concepts of zero potential control are somewhat counterintuitive to contemporary Spc or Lean Sigma tools, they have nevertheless been nearby for nearly 100 years. The ironic part is that the point behind zero potential control is not to stop considering or recording statistical data, the point is to start using these methods and skills in a qoute solving manner. It is surely pointless and a waste of time to analyze every year data sets when troubleshooting a defect. It is much more beneficial to go and search for the fault as it occurs. However, this easy act - observation is not nearly as sophisticated as sexy lean sigma tools or Spc systems that are fully integrated with our servers for real time data analysis. The nice thing about data variety is that it tells us some vital information: what is the defect, where is the defect, how many defects are occurring, who's watch the fault occurred on, and many other easy data variety points. The problem with data is that it tells you practically nothing about what caused the defects to occur. Just because it happened on Joe's shift doesn't mean Joe is the cause. It may be that Joe wasn't trained correctly. Or maybe the load on the air compressor is greater on first shift than it is on second shift and Joe can never get the engine to control correctly. The easy fact is this, zero inventory doesn't mean we stop collecting inventory, it just means that we start inviting every man in the qoute solving process.
If you know somebody that is running surely zero inventories, chances are that zero problems are being solved. The institution not retention inventory has the same effect on workers that retention excess inventory does: managers must come down hard on workers to make things happen. retention the right whole of inventory and maintaining zero excess will help free up resources to smoothly move materials while presenting opportunities to solve the problems. Managers now must found great coaching skills so that they can get every person to solve daily problems that pop up.
Lean Math - supervision X Zero catalogue = Zero question SolvingChelsea Fan Club and Goals World Cup News Blog Belkin G Wireless Router